Natural Beauty!
The elegant look of a hardwood floor can add warmth and character
to any room in a home. The natural characteristics of wood
add depth and a visual appearance that many other types of
floors try to duplicate. As the consumer demand for hardwood
floors has grown so has the manufacturer's ability to produce
better quality finishes and superior construction techniques.
With these advancements wood floors can now be installed
throughout the home and over a wide variety of subfloors.
Today, homeowners looking to use wood floors have the option
of purchasing three different types of wood flooring. Although
the end results may look the same there are distinct advantages
for using each type under different situations.
- 3/4" Solid Wood Floors
- Engineered Plank Floors
- Longstrip Plank Floors
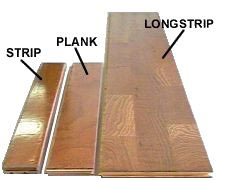
Once installed it is extremely difficult to tell the difference between a solid
wood floor and the other wood floors. Both the engineered and the longstrip have
thin layers of wood that are glued together. By gluing the plies together you
get better dimensional stability within the plank itself, which allows these
floors to be used on job sites that have a higher percentage of moisture content
than normal. This includes basements and over concrete slabs where solid strip
wood floors are considered off limits.
Another choice you have today is whether to go with a pre-finished wood floor,
or an unfinished wood floor. The pre-finished floors offer a wider variety of
wood species and saves hours of labor and cleanup. While the unfinished wood
floors allow you to have a custom job-site finish and the chance to level the
surface of the entire floor after it has been installed. You also get an extended
factory finish warranty with pre-finished floors, but not with most job-site
finishes.
Types of Wood Floors
Solid Flooring —
Regardless of width or length all wood flooring that is one piece of wood
from top to bottom is considered solid flooring. Solid flooring gives you a
great opportunity for customization of species, stains, and finishes all contributing
to the personalization of a solid floor.
Engineered Flooring — This wood flooring is available in
3 and 5 ply and consists of layers of wood pressed together, with the grains
running in different directions. Engineered
flooring is great for those areas of the house where solid wood flooring may
not be suitable such as a basement or kitchen. It is also more dimensionally
stable than solid wood.
Acrylic Impregnated Floors — This is a process in which the
acrylics are injected into the wood itself making it a extremely durable floor.
This type of flooring is often used in
commercial areas like shopping malls and restaurants but also work well in
busy households.
Wood Flooring - Surface Finishes
With today’s wood flooring finishes lasting beauty requires minimal
care. These finishes are usually urethanes and remain on the surface of the
wood and form a protective coating. They are also popular today because they
are water-resistant, durable, and require minimal maintenance.
Oil-modified urethane — is a solvent-base polyurethane that dries in about
eight hours and is easy to apply. This type of finish ambers.
Moisture-cured urethane — is also a solvent-based polyurethane
that is more durable and more resistant than other surface finishes. Moisture-cure
urethane
comes in non-yellowing and amber types and generally come in satin or gloss.
These finishes are extremely difficult to apply, has a strong odor and should
be applied by a professional.
Conversion varnish — is durable and dries clear to slight amber. These finishes
have a strong odor and should also be applied by a highly skilled flooring
professional.
Water-based urethane — finishes are clear and non-yellowing. They have a milder
odor and dry in about two to three hours.
Penetrating Stain and Wax — this finish soaks into
the pores of the wood and hardens to form a protective penetrating seal. The
wax gives
a low-gloss satin
sheen. It is generally maintained with solvent-based waxes, buffing pastes
or cleaning liquids (specifically for wax-finished wood floors) and an additional
thin application of wax as needed.
Ease of Maintenance
New technology in stains and finishes makes today’s wood floors easy
to maintain. Regular cleaning that takes little more than sweeping and/or vacuuming,
with occasional use of a professional wood floor cleaning product recommended
by your flooring manufacturer or installer is all it takes. This will ensure
that you use the proper cleaner for your type of flooring and finish.
Ecological
Wood floors are ecologically friendly. Since it is a natural resource, wood
is both renewable and recyclable. And because wood does not collect dust and
other allergens leading health associations agree that would floors are the
perfect choice for a healthy home.
Affordable
Today’s wood floors are affordable. Over time, wood floors maintain
their value.
Variety
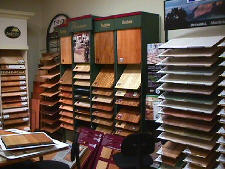
Today, there are more styles, colors and species of wood flooring available than
ever before. Whether you’re looking for traditional Pine or exotic Wenge,
you’re sure to find a color and style to fit you décor.
Atlanta Flooring Design Centers also sell and install real hardwood. Hardwood
flooring is a natural for you when you are considering replacing your floor
in the living room or your entry way. It also can be combined with carpet and
other types of flooring to provide a contrasting look to meet your unique requirements
Atlanta Flooring Design Centers offer a very broad selection of real hardwood
products from the leading manufacturers in the industry. These products are already
finished and can be installed quickly to replace your existing floor covering. We carry wood by Bruce, Hartco, Harris Tarkett, Robbins, Anderson, Mannington,
and Zickgraf.
No matter what type of wood you prefer we carry Pine, Red Oak, White Oak, and
specialty products such as Maple, Cherry, Walnut, Pecan, and Rosewood. We offer
products for any application, residential or commercial and a vast selection
of colors and styles. Even custom designs are made available by our installers.
Board samples are available for check-out to help make the selection of fine
wood flooring even easier.
Plank Edge Styles
Hardwood floors come in either a beveled edge, or a square edge. Today, most
hardwood floor manufacturers are calling their beveled edge "eased edge" because
the tapered edge is dramatically reduced from the old deeply grooved edges. The
beveled edges do serve a purpose. The manufacturer can produce beveled edge planks
faster than square edge, which in turn lowers their production costs. Also, a
beveled edge floor is more forgiving when installed over irregular subfloors
and you don't have the problem of overwood.
Square
Edge
|
The edges of all boards meet squarely
creating a uniform, smooth surface that blends the floor together from board
to board. The overall look of this floor gives a contemporary flair and
formal feeling to the room. |
Eased
Edge
|
Each board is just slightly
beveled. Some manufacturers add an eased edge to both the length of the
planks as well as the end joints. Eased edges are used to help hide minor
irregularities, such as uneven plank heights. Eased edge is also called
microbeveled edge. |
Beveled
Edge
|
These products
have a very distinctive groove in them. Beveled edge
planks lend themselves to an informal and country decor.
With the urethane finishes applied at the factory today
the beveled edges are sealed completely making dirt and
grit easy to be swept or vacuumed out of the grooves.
Beveled edge floors help hide subfloor irregularities
that could result in variations in board height, or “overwood”. |
Wood Species Relative Hardness Table
Below are listed the relative hardness for numerous wood species
used in flooring. These ratings were done using the Janka Hardness
Test, which measure the force needed to embed a .444 inch steel
ball to half its diameter in a piece of wood. The higher the
number the harder the wood. Although this is one of the best
methods to measure the ability of wood species to withstand
indentations, it should be used as a general guide when comparing
various species of wood flooring. The construction and finish
also play an important role in the durability and ease of maintenance
of any wood floor.
Solid Wood Floors
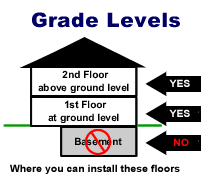
When we think of solid wood floors we generally are talking about a 3/4" thick
plank that is 2 1/4" wide. This is the classic strip wood floor, although
it is possible to find a narrower width or a slightly thinner guage. The strips
are generally in random lengths from 12" – 84". The most common
wood species used for solid strip floors are red oak, white oak, and maple.
Solid wood floors are one solid piece of wood that have tongue and groove
sides and come in either prefinished or unfinished styles. Solid wood floors
are sensitive to moisture and it is not recommended to install these floors
below ground level, or directly over a concrete slab. These floors are for
nail-down installations only. You can refinish, or recoat solid wood floors
several times, which adds to their appeal and to their long life. There are
solid floors that are over 100 years old and are still in good condition.
All
solid wood floors will react to the presence of moisture. In the winter months,
moisture leaves the wood causing the floor to contract which leaves unsightly
gaps between each plank. In the summer months when the humidity is higher the
wood will expand and the gaps will disappear. If there is too much moisture
it may cause the wood planks to cup, or buckle. This is why it is important
when installing a solid strip floor to leave the proper expansion area around
the perimeter and to acclimate the wood prior to installation.
When we talk about unfinished wood we generally think of solid wood floors.
Although there are many prefinished 3/4" solid wood floors too. Unfinished
solid oak floors come in several different qualities. These qualities are clear,
select and better, #1 common, and #2 common. The clear has no visual blemishes
or knots and is extremely expensive. The select and better quality has some
small knots and very little dark graining, while the #1 common and #2 common
have more knots and more dark graining. When buying an unfinished solid oak
floor make sure you know which quality you are buying.
Engineered Plank Floors
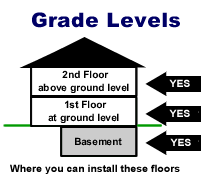
Engineered wood floors are generally 2,3, or 5 thin sheets of wood that are
laminated together to form one plank. These floors will range from 1/4" to
9/16" in thickness, and from 2 1/4" to 7" in width. The lengths
will be random and range from 12" – 60" in length. The top
finish layer can be cut from a variety of domestic or exotic hardwood species.
In the construction of engineered wood floors the wood plies are stacked on top
of each other but in the opposite directions. This creates a wood floor that
is dimensionally stable and less affected by moisture than a 3/4" solid
wood floor. This means you can install these floors over concrete slabs in basements,
as well as anywhere else in the home.
Wood always wants to expand in a certain direction. In the presence of moisture
solid wood planks will always expand across the width of the planks, rather than
down the length of the boards. To avoid this problem, manufacturers of engineered
planks place each ply in the opposite direction of each other. This is called
cross-ply construction. Once the wood layers are glued together the plies will
counteract each other which will stop the plank from growing or shrinking with
changes in the humidity. So if moisture is a concern then you should choose an
engineered type floor versus a solid strip floor.
Because engineered wood floors are made up of several layers of wood that are
all glued together it's possible to change the top finish layer to a totally
different wood specie without driving the costs out of sight. So if you want
to choose from a variety of domestic and exotic hardwoods than you should look
at an engineered wood floor.
Most engineered floors can be nailed down, stapled down, glued down, or floated
over a wide variety of subfloors, including some types of existing flooring.
You can also buy engineered floors in varying widths. They generally come in
2 1/4", 3", 5", and 7" widths and can be mixed, such as 3-5-7
inch planks installed side by side. By varying the board widths you can change
the total appearance of the floor.
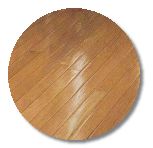 |
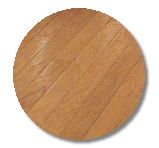 |
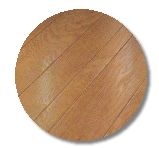 |
STRIP FLOORING
2 1/4" width
traditional linear look |
PLANK FLOORING
3" width
casual elegance |
RANDOM FLOORING
3", 5", 7" widths
more patterned look |
Longtstrip Plank Floors
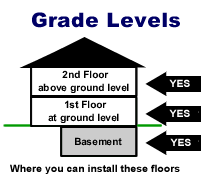
Longstrip floors are similar to engineered floors and have several
wood plies that are glued together. The center core is generally a softer wood
material and is used to make the tongue and groove. A hardwood finish layer is
glued on top of the core. The top layer can be almost any hardwood specie and
is made up of many smaller individual pieces that are laid in three rows. Longstrip
planks are approximately 86" in length and 7 1/2" in width. They generally
have between 17 and 35 pieces that make up the
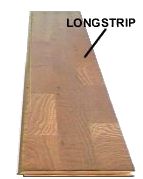
top layer of each board. This
gives the effect of installing a board that is 3 rows wide and several planks
long. Each longstrip plank looks like an entire section that has already been
pre-assembled.
Longstrip planks are designed for the floating installation, but most can
also be glued-down, or stapled down. Because these floors can be floated they
can go over a wide variety of subfloors and on any grade level. Like engineered
floors, longstrip floors come in a wide variety of domestic and exotic hardwood
species.
Wood Floor Finishes
The days of having to wax and scrub your hardwood floors are pretty much gone
forever. Manufacturers of prefinished wood floors have developed techniques to
quickly apply hard, durable, urethane based finishes right at the factory. By
using ultra violet lights the prefinished wood planks can have several coats
of urethane applied within a matter of a few minutes. This is helping make hardwood
floors both more affordable, and much easier to maintain. Recently, the hardwood
flooring manufacturers have begun to add small chips of Aluminum Oxide directly
to the floor's finish which dramatically increases the life of the urethane finish.
Most factory finished hardwood floors have several coats of finish applied
to the wood's surface. As example, many wood floor companies are applying 6-10
coats of a ultra-violet (UV) cured urethane. This would be extremely difficult
for someone to duplicate on a job site finish, not to mention how many days
it would take. This is one of the reasons why many flooring mechanics, flooring
retailers, and builders are pushing prefinished hardwood floors. Instead of
taking several days to install and finish a new hardwood floor a prefinished
hardwood floor is generally done in one day.
This does not mean you should wash your floor with a mop, but it does mean
these floors won't watermark like the old waxed hardwood floors. The the UV
cured urethane wood finishes do make these floors easier to maintain than the
old waxed hardwood floors.
Factory Prefinished Hardwood Flooring
Wood floors that have been factory finished before they are installed.
UV-cured – Factory finishes that are cured with Ultra Violet lights versus
heat.
Polyurethane – A clear, tough and durable finish that is applied as
a wear layer.
Acrylic-urethane – A slightly different chemical make up than Polyurethane
with the same benefits.
Ceramic – Advanced technology that allows the use of space-age ceramics
to increase the abrasion resistance of the wear layer.
Aluminum Oxide – Added to the urethane finish for increased abrasion
resistance of the wear layer, which is becoming extremely popular on the better
grade wood floors.
Acrylic Impregnated – Acrylic monomers are injected into the cell structure
of the wood to give increased hardness and then finished with a wear layer
over the wood.
Job-site Finished Hardwood Flooring
If you want a custom stained hardwood floor, or a wood floor to match existing
trim than a job-site finish is your answer. Job-site finish means you start with
a bare (unfinished) hardwood floor and than the floor is sanded, stained, and
finished in the home. The other advantage of a job-site finish is if you are
concerned with uneven heights between planks, the sanding process will smooth
out the floor. Be warned, this can be quite a mess and the process does take
several days.
Water Based Urethane – Water is used as part of the chemical make up
of the polyurethane finish.
Solvent Based Urethane – Oil is used as part of the chemical make up
of the polyurethane finish.
Moisture Cured Urethane – A similar chemical make up as solvent based
urethanes but, this finish needs the humidity (moisture ) in the air to cure.
Installation Options
Nail Down – Typically used with the 3/4" solid products, however there
are adapters available for thinner flooring sizes as well. 2" nailing cleats
are used with a wood flooring nailer and mallet to attach the flooring to the
subfloor. Solid Strip floors or Plank floors can only be installed on wooden
subfloors on grade or above grade.
Staple Down – 1-1/2 to 2 inch Staples are used versus nailing cleats
to attach the wood flooring to the subfloor. A pneumatic gun is used to drive
the staple into the wood flooring and subfloor. This procedure is easier than
the nail down for do-it-yourself installations. Not all wood flooring manufacturers
recommend the same staple gun. Read the manufacturers installation manual to
assure you have the right staple gun and right size staples.
Glue Down – The recommended mastic or adhesive is spread on with the
proper sized trowel to adhere the wood flooring to the subfloor.
Engineered wood floors and parquets can be glued down. Solid strip floors
and plank floors can only be nailed or stapled. There are many types of adhesives
on the market, please use the manufacturers recommended adhesive when installing
their flooring. Not using the manufacturers recommended adhesive and trowel
size could void any warranties you may have.
Floating – With the floating installation method the floor is not mechanically
fastened to any part of the subfloor. There is a thin pad that is placed between
the wood flooring and the subfloor. A recommended wood glue is applied in the
tongue and groove of each plank to hold the planks together. The padding protects
against moisture, reduces noise transmission, softer under foot, and provides
for some additional "R" value. Some engineered floors and all Longstrip
floors can be floated. This is a very fast, easy and clean method of installation.
Please consult the manufacturer installation instructions to see if your flooring
can be floated.